PCB & PCBA Manufactring Center
WITH prototypes, manufacturing, kitting, assembly and production included, we offer complete electronic assembly solutions. We have a complete range of electronic component placement devices, soldering equipment, and specialized electronic assembly instruments that deliver productive and top quality prototyping, small-to-mid-scale PCB manufacturing, entire kitting, assembly, and production capabilities.
OUR list of printed circuit board assembly capabilities allows our customers to have the convenience of a “One-Stop Service” for their manufacturing and assembly needs.
Main Production & Inspection Equipments (8 SMT LINE 3DIP LINE)
Equipment Name | Model | Manufactured by | Quantity We Have | Remarks |
---|---|---|---|---|
Full Automatic Screen Printer | DSP-1008 | DESEN | 8 | |
SMT Machine | YV88 | YAMAHA | 4 | 8 SMT Lines |
SMT Machine | YG100XGP | YAMAHA | 18 | |
SMT Machine | YV100XG | YAMAHA | 3 | |
SMT Machine | YG200 | YAMAHA | 5 | |
Reflow Soldering | 8820SM | NOUSSTAR | 4 | |
Reflow Soldering | XPM820 | Vitronics Soltec | 3 | |
Reflow Soldering | NS-800 II | JT | 1 | |
Solder Paste Inspection | REAL-Z5000 | REAL | 1 | |
Automatic Optical Inspection System | B486 | VCTA | 3 | |
Automatic Optical Inspection System | HV-736 | HEXI | 5 | |
X-Ray | AX8200 | UNICOMP | 1 | |
BGA Re-work | MS8000-S | MSC | 1 | |
Universal 4*48-pin drive concurrent multiprogramming system | Beehive204 | ELNEC | 3 | |
Automatic Plug-In machines | XG-3000 | SCIENCGO | 2 | |
Automatic wave soldering system | WS-450 | JT | 1 | 3 DIP Lines |
Automatic wave soldering system | MS-450 | JT | 2 |
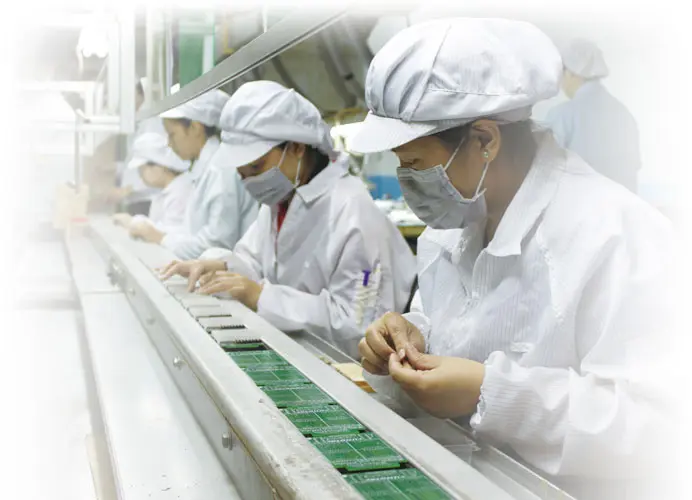
SATECH has 3 DIP lines. Benefiting from technical workbenches, rail cars and carriers, the DIP efficiency is immensely promoted so that the yield is up to 150,000,000 points per day. By reasonable KPI for the workers and the process manager, we optimize the DIP lines aiming at promoting the percent of pass up to 99.8%.
FOR the quality control, firstly our DIP team always analyze the quality condition of PCBs which the client provided and propose some suggestion on optimization in DIP craft. Then the PE engineers need to make series of tests for the oven temperature in wave-soldering, scaling powder, the gradient, transfer rate and preheating zone and so on to fix up the best DIP quality. Finally they even make some special jigs to make sure the PCB passes through wave-soldering, as you know, this can protect the PCB in the whole wave-soldering.
SMT Processing
QC for PCB SMT Service
SATECH always attach importance to the quality of SMT processing, so we always comply with the international IPC acceptance standard and ISO9001 SMS to strictly implement SOP work flow and execute IQC & IPQC properly, therefore, in our SMT lines, some common problems such as cold solder joint and material wastage can be under effective control. Now we are proud to be the well-known professional SMT processing lines in whole Shenzhen.
- Material Checking: the quality of material is decisive for the lifetime of PCB.
- Solder-paste Checking: we always checkout, unfreeze and stir before using the solder paste from well-known brand SMIC.
- Stencil & Scraper Control: the stencil is in constant-temperature preservation and made tension test before using. The using of a scraper is able to be precisely controlled in an angel of 45, and it will be scrapped after being using in limited times.
- SMT Modulation & First QC: after modulating the SMT machines to make sure of mounting precision as the client provided the coordinate files, then we make the first QC to produce in bulk.
- Reflow Soldering Control & Second QC: after SMT, the reflow soldering is proceeded and modulated the reflow temperature according to the PCB plate and some special components and parts . Meanwhile, before volume production we make the second QC to avoid that the solder paste is dissolved and components & parts becomes yellow or cold joint.
- Third QC: QA workers sample the finished PCB and then parcel up to deliver.